Australia’s construction sector stands on the cusp of a significant transformation fueled by technological innovations. As a cornerstone of the economy, the construction industry in Australia has historically been vital, yet it has faced challenges regarding productivity, sustainability, and efficiency. However, in recent years, the infusion of cutting-edge technologies has begun reshaping traditional practices, propelling the sector into a new era of innovation and modernization. This blog will delve into the multifaceted role that technology plays in revolutionising and modernising Australia’s construction industry.
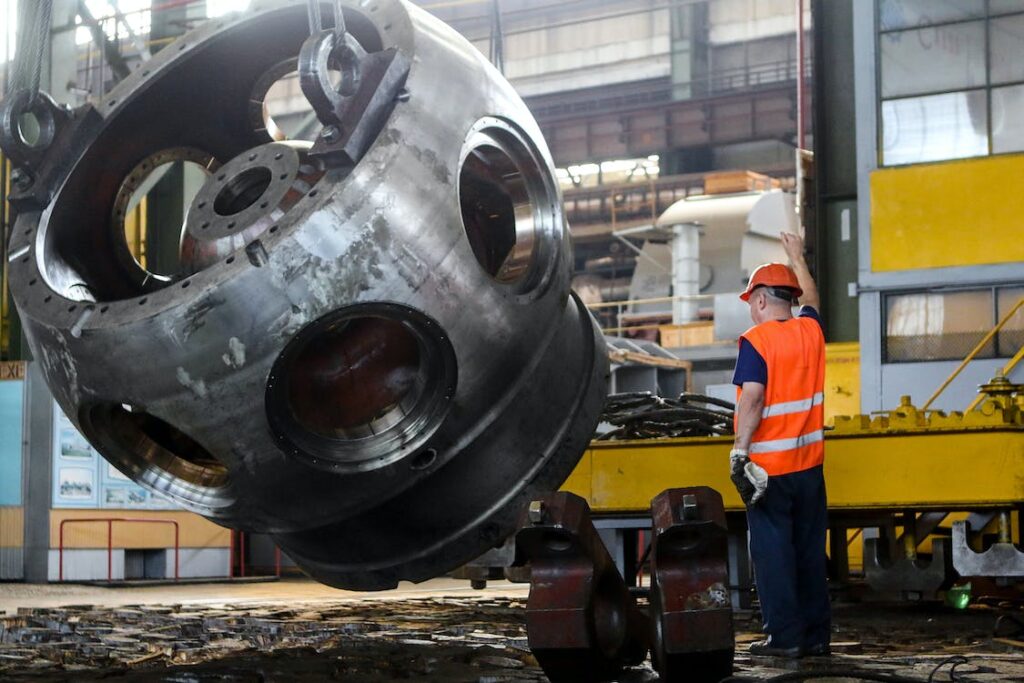
Building Information Modeling (BIM) and Digital Twins
Building Information Modeling (BIM) serves as a revolutionary catalyst in reshaping the construction landscape, acting as a digital cornerstone that revolutionises how projects are conceived, executed, and managed. At its core, BIM isn’t merely a software tool; it’s a transformative approach that transcends traditional construction methodologies. This digital framework acts as an intricate nexus, seamlessly integrating diverse facets of a construction project, spanning from the earliest conceptualization stages through design, construction, and even post-completion phases.
One of the primary strengths of BIM lies in its ability to create comprehensive 3D models that encapsulate the entirety of a structure. These models aren’t just static representations; they serve as dynamic, data-rich environments that capture not only the visual aspects but also the intricate details, specifications, and functionality of every component within the building. This comprehensive model acts as a central repository of information, fostering a collaborative environment where architects, engineers, contractors, and stakeholders can converge, contributing their expertise and insights to refine the project.
The advantages of BIM reverberate throughout the project lifecycle. During the design and planning phases, stakeholders can visualise the structure in three dimensions, enabling better comprehension of spatial relationships and potential clashes between systems or elements. This enhanced visualisation mitigates errors and conflicts at the outset, streamlining the planning process and ensuring a smoother transition to the construction phase.
BIM also facilitates interdisciplinary collaboration, breaking down silos that traditionally hindered communication among different stakeholders. Architects, engineers, and contractors can work in tandem, accessing the same model to coordinate designs, identify clashes, and resolve issues collaboratively. This synergy fosters an environment where decisions are informed by real-time data and collective insights, optimising efficiency and minimising costly rework.
However, BIM’s impact transcends the construction phase; it extends into the realm of facility management and beyond with the advent of digital twins. These virtual replicas of physical structures provide stakeholders with a dynamic platform to simulate, monitor, and optimise operations even after construction completion. Digital twins harness real-time data from sensors and IoT devices embedded within the physical structure, enabling stakeholders to monitor performance metrics, predict maintenance needs, and fine-tune operations to enhance efficiency and longevity.
For instance, facility managers can leverage digital twins to simulate various scenarios, analysing how changes in occupancy, usage patterns, or environmental conditions might impact a building’s performance. This foresight allows for proactive maintenance, optimising energy consumption, and ensuring optimal functionality, thereby prolonging the building’s lifespan and reducing operational costs.
Therefore, the integration of BIM and the emergence of digital twins represent a paradigm shift in the construction industry—a shift from fragmented, paper-based processes to a cohesive, data-driven approach. This digital transformation not only revolutionises how buildings are designed and constructed but also empowers stakeholders to optimise performance, maximise efficiency, and ensure sustainability throughout a structure’s entire lifecycle. Ultimately, BIM and digital twins epitomise the convergence of technology and construction, ushering in an era where buildings are not just structures but living entities, continuously evolving and adapting to meet the demands of the future.
Impact of BIM:
Enhanced Collaboration: BIM fosters seamless collaboration among architects, engineers, contractors, and other stakeholders, mitigating errors and conflicts during the planning and execution phases.
Efficiency and Cost Reduction: By enabling precise planning and visualisation, BIM minimises rework, optimises resource allocation, and reduces overall project costs.
Examples:
Sydney Opera House’s BIM Implementation: Renowned structures like the Sydney Opera House have embraced BIM for efficient management and maintenance, showcasing its potential in heritage preservation and modern facility management.
Prefabrication and Modular Construction
Prefabrication and modular construction techniques have swiftly emerged as transformative approaches within Australia’s construction industry, heralding a new era characterised by efficiency, sustainability, and innovation. These methodologies represent a departure from conventional on-site construction practices, revolutionising the building process through the strategic fabrication of building components in off-site, controlled environments.
At the core of prefabrication lies a strategic shift towards standardisation and precision. Through meticulous planning and design, standardised building components are crafted within factory settings. This methodical approach ensures consistency and uniformity in the production of these elements, mitigating variations that often arise in traditional on-site construction. The result is an assembly line-like process where components, ranging from wall panels and floor systems to entire room modules, are manufactured with unparalleled precision.
The advantages of prefabrication reverberate across various facets of the construction process. One of its primary benefits is the dramatic reduction in construction timelines. By fabricating components concurrently with on-site preparations, construction schedules are significantly compressed. Once these prefabricated components reach the construction site, the assembly process is streamlined, minimising the time needed for on-site construction. This acceleration in timelines not only expedites project completion but also minimises disruptions to surrounding environments, reducing inconvenience to nearby communities.
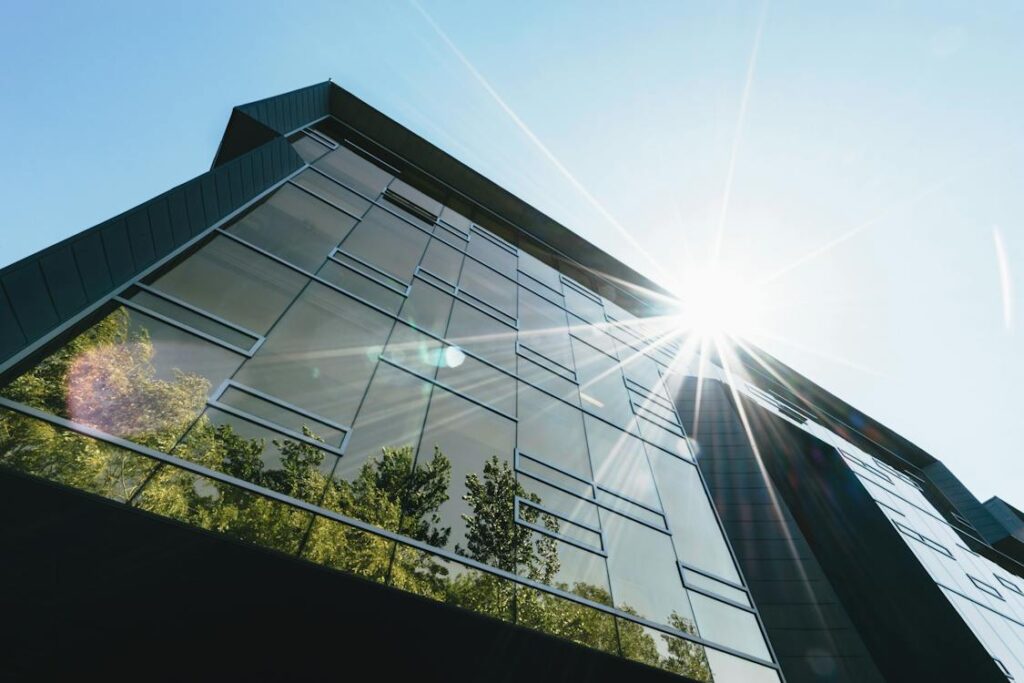
Furthermore, the controlled factory environment in which prefabrication occurs leads to enhanced quality control. Rigorous quality assurance protocols govern the manufacturing process, ensuring that every component meets stringent standards. This meticulous oversight significantly reduces the incidence of defects or errors often encountered in conventional on-site construction. The result is a higher-quality end product, bolstering durability, and reducing the likelihood of rework or corrective measures.
Additionally, prefabrication aligns closely with sustainability objectives by minimising material wastage. The precision-driven nature of this technique optimises resource utilisation, as materials are meticulously measured and utilised according to exact specifications. Excess waste commonly associated with traditional construction methods, such as leftover materials or offcuts, is dramatically reduced. This not only contributes to cost savings but also aligns with eco-conscious practices, reducing the environmental impact of construction activities.
Further, the modular nature of prefabricated components offers unparalleled flexibility in design and customization. Architects and builders can harness this flexibility to create innovative, tailored solutions, catering to diverse project requirements while maintaining efficiency and consistency in the construction process.
To summarise, prefabrication and modular construction techniques represent a pivotal shift in the construction paradigm, optimising efficiency, quality, and sustainability. By leveraging controlled environments, standardised components, and streamlined assembly processes, these methodologies not only expedite construction timelines but also lay the groundwork for a more sustainable and adaptable construction landscape in Australia. As these techniques continue to gain prominence, their integration into the construction sector signifies a transformative evolution toward more efficient, cost-effective, and environmentally conscious building practices.
Advantages of Prefabrication:
Speed and Efficiency: Prefabrication significantly accelerates construction timelines, enabling faster project completions and reducing disruptions at the site.
Quality Control: Controlled factory conditions ensure higher quality standards and uniformity in building components, minimising errors and defects.
Examples:
Modular Housing Projects: Initiatives like modular housing projects in Melbourne and Sydney have showcased the viability of prefabrication in delivering affordable, high-quality housing solutions.
Robotics and Automation
The integration of robotics and automation in construction processes marks a pivotal shift towards increased efficiency and safety. Autonomous vehicles, drones, and robotic systems are revolutionising various tasks within construction, ranging from site surveying and material handling to bricklaying and even demolition. These technologies not only expedite processes but also enhance precision, mitigate risks, and reduce labour-intensive tasks.
Impact of Robotics:
Improved Safety: Robotics and automation minimise human involvement in hazardous tasks, thereby enhancing safety on construction sites.
Precision and Speed: Robotic systems execute tasks with unparalleled precision and speed, boosting productivity and minimising errors.
Examples:
Drones for Site Monitoring: Drones equipped with cameras and sensors are employed for site surveys, progress monitoring, and inspecting hard-to-reach areas, improving project oversight and efficiency.
Sustainability and Renewable Energy Integration
Technology plays a pivotal role in fostering sustainability within Australia’s construction sector. From advancements in eco-friendly building materials to the integration of renewable energy solutions like solar panels and energy-efficient designs, the industry is witnessing a shift towards greener practices. Sustainable construction materials, such as recycled steel, timber, and eco-friendly concrete alternatives, contribute to reducing the environmental footprint of construction projects.
Advancements in Sustainability:
Green Building Certifications: Initiatives like Green Star and NABERS assess and certify buildings based on their sustainability and energy efficiency, encouraging the adoption of green practices.
Renewable Energy Integration: The incorporation of solar panels, energy-efficient lighting, and HVAC systems reduces buildings’ reliance on conventional energy sources.
Examples:
Green Building Initiatives: Projects like the Barangaroo South precinct in Sydney, awarded a 6-Star Green Star rating, exemplify sustainable urban development by integrating renewable energy sources and eco-friendly designs.
The infusion of technology into Australia’s construction sector heralds a transformative era, redefining traditional practices and unlocking new realms of efficiency, sustainability, and innovation. From digital advancements like BIM and digital twins to the implementation of prefabrication, robotics, and sustainability initiatives, these technological interventions are reshaping the industry’s landscape. As Australia continues to embrace these innovations, the construction sector stands poised to evolve into a more efficient, sustainable, and technologically adept realm, laying the foundation for a future where buildings aren’t just structures but embodiments of cutting-edge progress and sustainability.
A good construction software makes use of good project management functionality, estimate and financial/accounting tool functionality, job management, scheduling and planning and support functionalities and more. WunderBuild is a construction management software that aims to provide all of these functionalities and more to bring out the best outcomes for a project. Enquire here today, to learn more about Wunderbuild and start your free trial.