The Australian building industry is undergoing a significant transformation, driven by the rise of modular construction. This innovative modular construction approach to building design and assembly is changing the way structures are constructed, offering numerous benefits over traditional methods. Modular construction involves creating building components in a factory setting before transporting them to the construction site for assembly. This blog explores the reasons behind the increasing popularity of modular construction in Australia, the benefits it offers, the challenges it faces, and its future prospects.
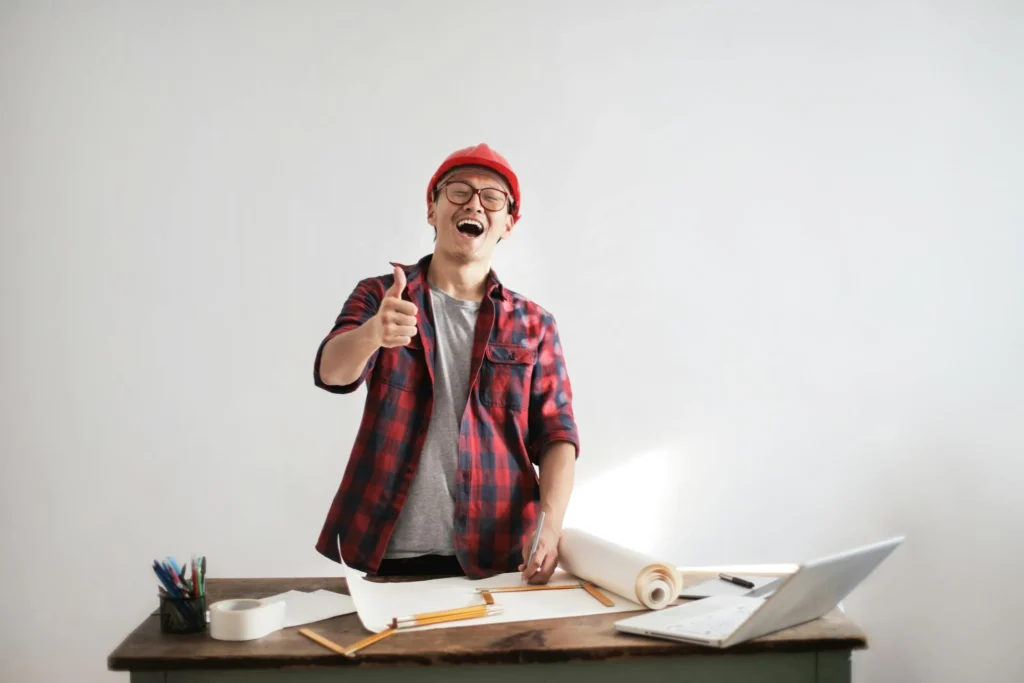
What is Modular Construction?
Modular construction, also known as prefabricated construction, involves producing sections of a building (modules) in a controlled factory environment. These modules are then transported to the construction site, where they are assembled to form a complete structure. This method contrasts with traditional construction, where buildings are erected entirely on-site from the ground up.
Why is Modular Construction Gaining Popularity?
Several factors are driving the rise of modular construction in Australia:
1. Efficiency and Speed
One of the primary advantages of modular construction is the significant reduction in construction time, a factor that has become increasingly crucial in today’s fast-paced building environment. Traditional construction methods typically follow a sequential process, where site preparation, foundation laying, structural framing, and finishing work occur one after the other, often leading to extended project timelines.
In contrast, modular construction revolutionises this approach by allowing multiple phases of the building process to happen simultaneously. By prefabricated building components in a factory setting, modules are produced concurrently with on-site activities such as site preparation and foundation work. This parallel processing is akin to an assembly line in manufacturing, where different parts of the product are assembled simultaneously, leading to a faster overall completion time.
For instance, while a construction crew is laying the foundation and preparing the site, the modules—whether they are sections of a residential building, office spaces, or even entire classrooms—are being built, fitted, and finished in a controlled factory environment. These modules are often 80-90% complete when they leave the factory, including all internal finishes, fixtures, and fittings. Once transported to the construction site, they are craned into place and swiftly assembled, dramatically reducing the on-site construction phase. This efficient workflow can cut overall project timelines by up to 50%, a remarkable improvement over traditional methods.
2. Cost-Effectiveness
Modular construction can be more cost-effective than traditional methods, offering a range of financial advantages that appeal to developers and investors alike. One of the primary reasons for this cost-effectiveness is the ability to leverage economies of scale within a factory setting. When building components are produced in large quantities in a controlled environment, manufacturers can purchase materials in bulk at discounted rates, significantly lowering the overall material costs. This bulk purchasing is particularly advantageous for large-scale projects where the savings on materials can be substantial.
Moreover, the factory environment allows for a high degree of precision and efficiency in the construction process. The use of advanced machinery and standardised procedures minimises material waste, as components are cut and assembled with exact specifications. In traditional construction, material waste can be considerable due to on-site errors, off-cuts, and damage from exposure to the elements. In contrast, the controlled conditions of a factory significantly reduce these issues, leading to more efficient use of resources and further cost savings.
The controlled environment also plays a crucial role in minimising weather-related delays and damage, which are common in traditional construction projects. On-site construction is highly susceptible to weather conditions such as rain, wind, and extreme temperatures, which can cause delays, damage materials, and increase labour costs. In a factory, however, production can continue uninterrupted regardless of external weather conditions, ensuring a more consistent and predictable construction schedule. This reliability translates to fewer unexpected costs and disruptions, making budget management more straightforward.
Additionally, the factory setting facilitates a high level of quality control, ensuring that each module is built to precise standards before it leaves the factory. This level of oversight reduces the likelihood of costly rework and repairs that can occur with traditional on-site construction. The consistent quality of factory-produced modules also means that buildings are often more durable and require less maintenance over their lifespan, contributing to long-term cost savings.
The predictability of factory production also enhances financial planning and budget management for construction projects. With traditional construction, unforeseen issues such as labour shortages, site conditions, and weather delays can cause significant budget overruns. In modular construction, the majority of the building work is completed in a controlled environment with predictable timelines and costs. This predictability allows for more accurate budgeting and financial forecasting, reducing the risk of cost overruns and enabling developers to secure financing more easily.
Furthermore, the speed of modular construction translates into financial savings through reduced interest payments on construction loans. Shorter construction timelines mean that developers can bring their projects to market more quickly, allowing for faster occupancy and revenue generation. This accelerated timeline can be particularly beneficial in markets with high demand for residential or commercial space, where getting a project completed and occupied quickly can result in a competitive advantage.
In addition to direct cost savings, modular construction can also lead to indirect financial benefits. For example, the reduced construction timeline can decrease the time developers spend managing the project, freeing up their resources to focus on other opportunities. The ability to complete projects more quickly can also enhance a developer’s reputation for efficiency and reliability, potentially leading to more business opportunities and partnerships in the future.
3. Quality Control
Building components are manufactured in a controlled factory environment, ensuring consistent quality and precision. Advanced manufacturing techniques and rigorous quality control processes reduce the likelihood of defects and enhance the overall durability and performance of the buildings. This results in higher standards of construction compared to on-site methods, where variables like weather and site conditions can impact quality.
4. Sustainability
Modular construction is inherently more sustainable than traditional construction. The factory setting allows for better waste management, recycling of materials, and reduction in energy consumption. Additionally, the precise manufacturing process ensures minimal material wastage. The modules can also be designed for energy efficiency, incorporating features like high-performance insulation and renewable energy systems, contributing to greener buildings.
Benefits of Modular Construction
The rise of modular construction offers several benefits to the Australian building industry:
1. Flexibility and Scalability
Modular construction allows for great flexibility in design and scalability. Modules can be customised to meet specific project requirements and can be easily expanded or modified. This makes modular construction ideal for a wide range of applications, from residential homes and apartment complexes to schools, hospitals, and commercial buildings.
2. Improved Safety
Construction work can be hazardous, with risks of accidents and injuries on-site. Modular construction improves safety by shifting much of the work to a controlled factory environment, where safety protocols are easier to enforce. This reduces the number of workers exposed to on-site hazards and contributes to a safer overall construction process.
3. Minimal Site Disruption
Traditional construction can cause significant disruption to surrounding areas, including noise, dust, and traffic congestion. Modular construction minimises these impacts by reducing the amount of on-site work and associated disturbances. This is particularly beneficial in urban areas where space is limited and disruptions can have broader social and economic effects.
4. Enhanced Building Performance
Modular buildings often exhibit better performance in terms of energy efficiency, thermal insulation, and acoustic properties. The precision manufacturing process ensures that each module is built to exact specifications, reducing gaps and inconsistencies that can lead to energy loss. This results in buildings that are more comfortable to live in and cheaper to maintain.
Challenges Facing Modular Construction
Despite its many advantages, modular construction faces several challenges that need to be addressed for its widespread adoption in Australia:
1. Perception and Acceptance
One of the significant hurdles for modular construction is the perception that it produces lower-quality or temporary structures. Educating stakeholders, including developers, architects, and potential buyers, about the benefits and capabilities of modular construction is essential to changing these perceptions.
2. Initial Costs and Financing
While modular construction can be cost-effective in the long run, the initial investment in factory setup, transportation, and specialised labour can be higher. Securing financing for modular projects can also be challenging, as lenders may be more familiar with traditional construction models. Developing financial models and incentives to support modular construction is crucial for its growth.
3. Regulatory and Code Compliance
Navigating building codes and regulations can be complex for modular construction, as standards often vary between jurisdictions. Ensuring that modular buildings meet local building codes and obtaining necessary approvals can be time-consuming. Streamlining regulatory processes and updating codes to accommodate modular construction can help overcome this challenge.
4. Logistics and Transportation
Transporting large modules from the factory to the construction site involves logistical challenges, including securing permits, managing transportation routes, and ensuring modules are not damaged during transit. Developing efficient logistics and transportation strategies is essential for the smooth implementation of modular construction projects.
Case Studies of Modular Construction in Australia
1. The Hive, Melbourne
The Hive is a modular apartment complex in Melbourne that showcases the potential of modular construction for residential buildings. The project consists of 20 apartments, each constructed from prefabricated modules assembled on-site in just five days. The Hive demonstrates how modular construction can provide high-quality, affordable housing solutions in urban areas.
2. Monash University, Clayton Campus
Monash University has embraced modular construction for several of its buildings on the Clayton campus. The Gillies Hall student accommodation is a notable example, featuring 150 prefabricated modules. The building is designed for energy efficiency and sustainability, incorporating features like solar panels and rainwater harvesting systems. This project highlights the versatility of modular construction for educational facilities.
3. Modular Schools in New South Wales
The New South Wales government has implemented a modular school building program to address the growing demand for educational facilities. Modular classrooms and buildings are being deployed across the state to provide high-quality, rapid-build solutions for schools. This initiative demonstrates how modular construction can address urgent infrastructure needs in the education sector.
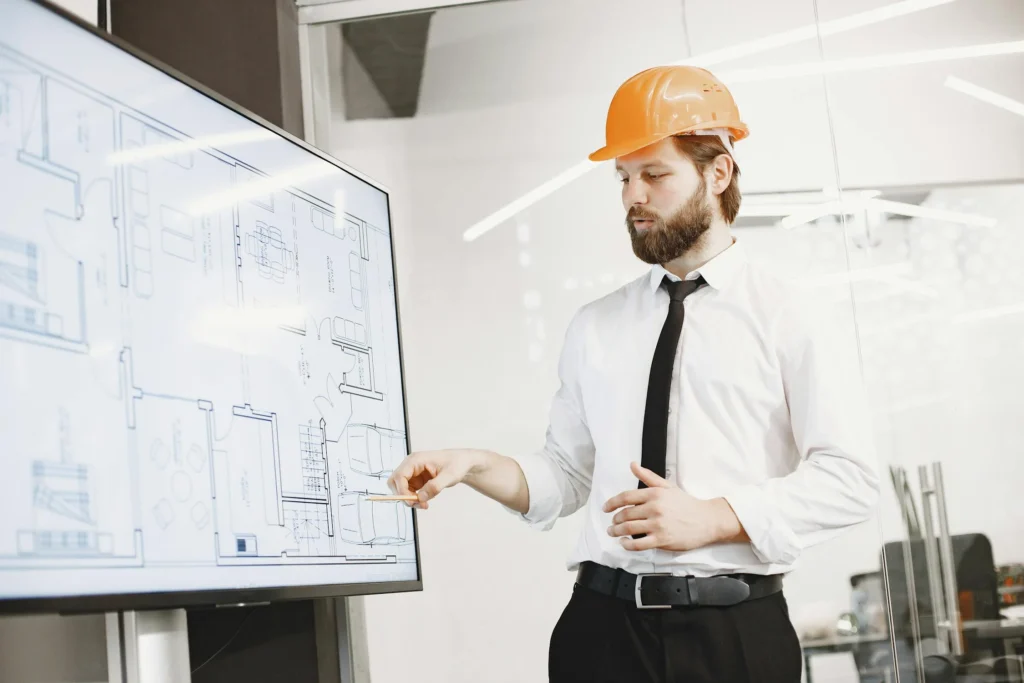
The Future of Modular Construction in Australia
The future of modular construction in Australia looks promising, with several trends and developments likely to shape its growth:
1. Technological Advancements
Advances in digital technologies, such as Building Information Modeling (BIM), are enhancing the design and construction of modular buildings. BIM allows for precise planning, visualisation, and coordination of modular components, reducing errors and improving efficiency. Additionally, advancements in automation and robotics are streamlining the manufacturing process, further increasing the speed and quality of modular construction.
2. Government Support and Policy
Increased government support and favourable policies can drive the adoption of modular construction. Initiatives like grants, tax incentives, and streamlined regulatory processes can encourage developers to embrace modular methods. Government-led projects, such as public housing and infrastructure, can also serve as catalysts for the broader adoption of modular construction.
3. Sustainability and Green Building
As sustainability becomes a central focus in the construction industry, modular construction’s green credentials will become increasingly important. The ability to integrate sustainable materials, renewable energy systems, and energy-efficient designs makes modular construction an attractive option for eco-conscious developers and buyers. The growing demand for green buildings will likely drive further innovation and adoption of modular construction practices.
4. Urbanization and Population Growth
Australia’s population is projected to continue growing, with significant urbanisation expected in major cities. Modular construction offers a viable solution to meet the housing and infrastructure needs of expanding urban populations. Its speed and efficiency make it well-suited to address the pressures of rapid urbanisation and the need for affordable housing.
The rise of modular construction in the Australian building industry represents a significant shift towards more efficient, cost-effective, and sustainable building practices. While challenges remain, the benefits of modular construction are clear, and its potential to transform the industry is immense. As technological advancements continue, and with increasing support from government and industry stakeholders, modular construction is poised to play a crucial role in shaping the future of Australia’s built environment. The integration of smart technologies, sustainable practices, and innovative design will ensure that modular construction meets the evolving needs of communities and contributes to a more resilient and prosperous Australia.
Streamline your construction projects with Wunderbuild, a leading software for enhancing efficiency and collaboration. Discover here how Wunderbuild can help you deliver projects on time and within budget.