The construction industry has seen a significant shift in recent years, with modular construction emerging as a viable alternative to traditional methods. Modular construction involves the fabrication of building components, or “modules,” in a controlled factory environment before assembling them on-site. This innovative approach has gained popularity for its potential to streamline construction processes and improve efficiency. In this blog, we will explore the advantages and limitations of modular construction, shedding light on how this method is reshaping the industry.
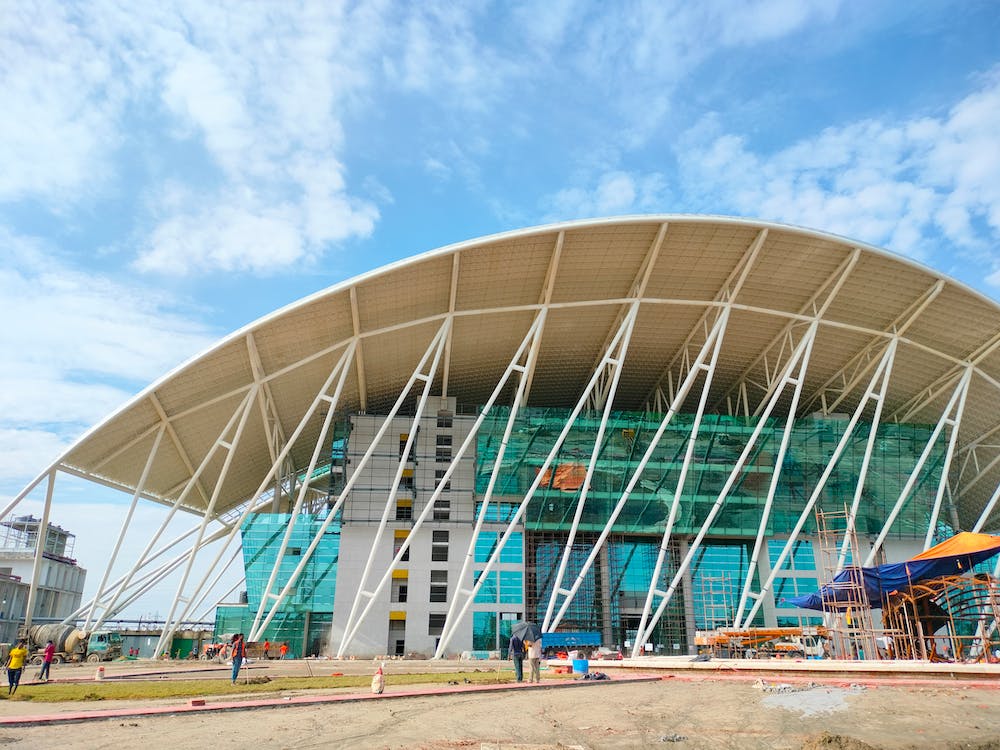
Advantages of Modular Construction
1. Speed and Efficiency
The capability of modular construction to expedite project timelines is a game-changer in the construction industry. This advantage not only benefits developers and construction firms but also addresses critical needs in various scenarios explained below.
In the aftermath of natural disasters such as hurricanes, earthquakes, or floods, there is an urgent need for temporary housing and facilities for affected populations. Modular construction’s ability to rapidly produce and assemble building modules becomes invaluable in these situations. Emergency housing units, medical clinics, and schools can be deployed quickly, providing shelter and essential services to those in need.
Many urban areas around the world are experiencing rapid population growth, driven by factors such as rural-to-urban migration and economic opportunities. In these cases, the demand for housing, schools, healthcare facilities, and infrastructure often outpaces the construction industry’s ability to deliver projects using traditional methods.
Modular construction offers a way to address this housing and infrastructure deficit promptly. By concurrently manufacturing modules while preparing the construction site, developers can keep pace with the accelerated urbanisation and ensure that essential facilities are available to support growing communities.
2. Improved Quality Control
Modules are constructed in a controlled factory environment, where quality control measures can be rigorously enforced. This controlled setting minimises the impact of adverse weather conditions, which often delay traditional construction projects and can compromise quality. As a result, modular buildings tend to have fewer defects and higher quality finishes.
3. Cost Savings
Modular construction can lead to cost savings in several ways. Reduced construction time translates to lower labour costs. Additionally, the controlled factory environment allows for better resource management and waste reduction. Furthermore, the efficiency of the modular process often leads to decreased overall project costs, making it an attractive option for budget-conscious developers.
4. Sustainability
Modular construction is inherently more sustainable than traditional construction methods. Precisely engineered modules result in less material waste. Additionally, the controlled factory environment allows for the integration of energy-efficient technologies and sustainable materials. Transporting modules to the construction site also reduces the need for on-site transportation, minimising the carbon footprint of the project.
5. Design Flexibility
Contrary to the misconception that modular buildings are limited in design, they can be highly customizable. Modular construction allows for the incorporation of various architectural styles, finishes, and layouts. Developers and architects have the flexibility to design unique, aesthetically pleasing structures while benefiting from the efficiencies of the modular process.
6. Reduced Site Disruption
Traditional construction projects can disrupt the surrounding environment and inconvenience local communities. In contrast, modular construction generates less on-site noise, traffic, and disruption. This is particularly beneficial when building in densely populated urban areas or sensitive locations.
7. Consistency and Replicability
Modular construction lends itself well to projects that require uniformity and replication. For example, hotel chains, student housing complexes, and residential developments can benefit from the consistent quality and design offered by modular construction. Developers can easily replicate successful designs in different locations, ensuring brand consistency.
8. Safety
Safety is a paramount concern in construction. The factory environment of modular construction minimises many of the safety risks associated with traditional on-site construction, such as accidents due to falls, heavy machinery, or adverse weather conditions.
Limitations of Modular Construction
While modular construction offers numerous advantages, it is not without its limitations. Understanding these limitations is crucial for making informed decisions about its applicability to specific projects.
1. Design Constraints
The design limitations inherent in modular construction are a topic that often comes up in discussions surrounding this innovative building method. While modular construction offers numerous advantages, including speed, efficiency, and cost savings, its reliance on predefined module sizes and shapes can indeed pose challenges when trying to achieve highly complex or non-standard architectural designs.
Modular construction relies on a degree of standardisation to maximise efficiency and cost-effectiveness. Standardised module sizes and shapes simplify the manufacturing process, enabling modules to be produced in a controlled factory environment with precision and consistency. This standardisation is what allows modular construction to offer its notable advantages.
When it comes to complex architectural designs that involve irregular shapes, intricate geometries, or non-standard building layouts, modular construction may face limitations. Achieving these designs may require customization or highly specialised modules, which can increase costs and complicate the manufacturing process.
Customising modules for unique architectural designs may involve design adjustments, which can be time-consuming and may introduce the risk of errors or delays. Additionally, customization can affect the interchangeability of modules, potentially limiting their reusability in future projects.
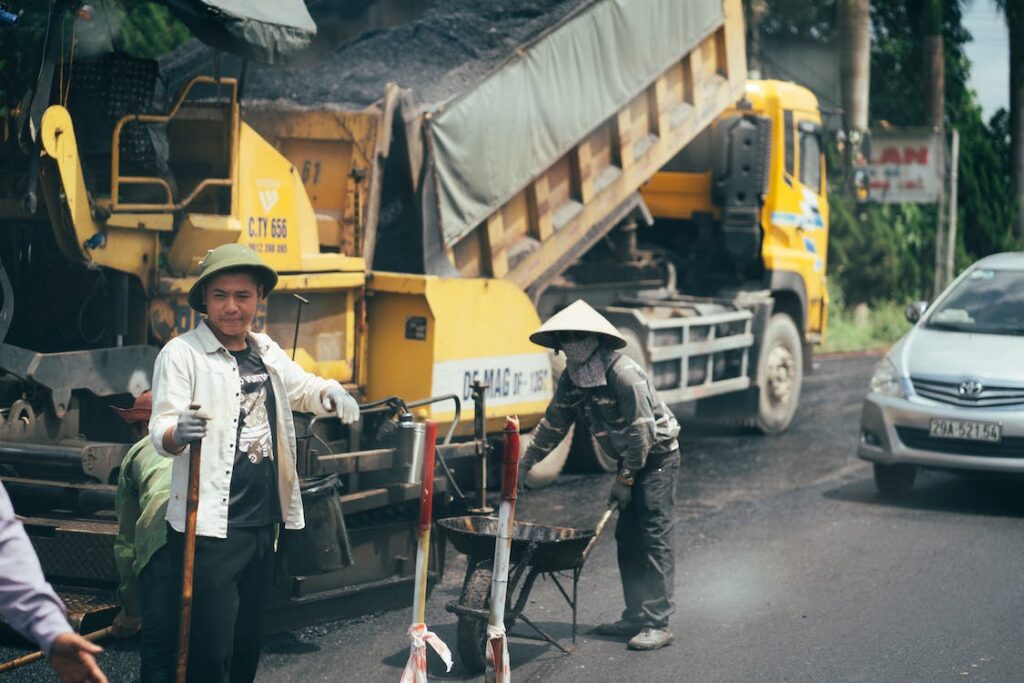
2. Transportation Costs
Transporting modular components to the construction site can be expensive, especially for projects located far from the factory. Oversized or overweight modules may require special permits and escort vehicles, adding to transportation costs. However, these costs can still be offset by the overall savings in labor and time.
3. Site Access and Space
The assembly of modular components requires adequate space and site access for cranes and other equipment. In congested urban areas or sites with limited access, modular construction may present logistical challenges. Site preparation and coordination are crucial to ensure a smooth assembly process.
4. Limited Material Variability
Modular construction relies on standardised materials and components. While this can lead to cost savings and quality control, it may limit the choice of materials for specific architectural or functional requirements. Developers must carefully consider the suitability of modular materials for their project.
5. Initial Investment
Setting up a modular construction facility requires a significant initial investment in infrastructure and equipment. Developers or construction firms looking to adopt modular methods need to weigh these startup costs against the long-term benefits of efficiency and cost savings.
6. Integration Challenges
In projects that require intricate mechanical, electrical, and plumbing (MEP) systems, integrating these systems within modular components can be complex. Ensuring seamless connections and functionality may require additional coordination and expertise.
7. Skilled Workforce
While modular construction reduces the demand for on-site labour, it places a premium on skilled workers involved in module fabrication and assembly. A skilled and specialised workforce is essential to ensure the quality and efficiency of modular projects.
8. Resistance to Change
The construction industry, steeped in tradition and accustomed to long-standing practices, often exhibits a degree of resistance to change. The adoption of modular construction methods, despite their numerous advantages, can indeed face scepticism and reluctance from various stakeholders who are more comfortable with conventional construction practices.
Tradition and established routines are deeply ingrained in the culture of the construction industry. Many professionals, from architects and engineers to contractors and labourers, have been trained and have honed their skills using traditional methods. This institutional inertia can make it challenging to embrace new approaches like modular construction, which may require relearning or adapting existing skill sets.
Change often brings with it a sense of risk and uncertainty. In the case of modular construction, stakeholders may worry about the potential pitfalls or unknowns associated with a different construction methodology. Concerns related to quality, durability, or project outcomes may lead to apprehension about adopting modular practices.
The construction industry has a long history of familiarity with traditional construction practices. Stakeholders may be less familiar with the principles, processes, and intricacies of modular construction. This lack of familiarity can breed hesitation, as people are generally more comfortable with what they know.
Examples of Successful Modular Projects
To illustrate the advantages and limitations of modular construction, consider these case studies:
1. Marriott’s AC Hotel in Oklahoma City
Marriott’s AC Hotel in Oklahoma City is an example of a successful modular construction project. The 142-room hotel was built using modular construction methods, allowing it to open its doors to guests more quickly. The project showcased the speed, efficiency, and quality control benefits of modular construction.
2. Forest City Ratner’s 461 Dean Street in Brooklyn
Forest City Ratner’s 461 Dean Street, a residential high-rise in Brooklyn, demonstrated the design flexibility of modular construction. The project featured modular units that combined to create a visually striking and unique building, challenging the notion that modular construction limits architectural creativity.
3. The Stack, London’s Tallest Modular Building
The Stack, a 28-story building in London, holds the title of the city’s tallest modular building. It showcases how modular construction can be used for complex, high-rise structures. Despite its height, the project was completed in less time than traditional construction methods would have allowed.
Modular construction is revolutionising the building industry by offering numerous advantages, including speed, quality control, cost savings, and sustainability. However, it also has its limitations, such as design constraints, transportation costs, and the need for a skilled workforce. To determine whether modular construction is suitable for a particular project, developers, architects, and construction firms must carefully evaluate its pros and cons in the context of their specific requirements.
As technology advances and the construction industry continues to evolve, modular construction is likely to play an increasingly significant role in meeting the growing demand for efficient, sustainable, and high-quality building solutions. By understanding both the advantages and limitations of modular construction, stakeholders can make informed decisions that lead to successful and innovative construction projects.
A good construction software makes use of good project management functionality, estimate and financial/accounting tool functionality, job management, scheduling and planning and support functionalities and more. WunderBuild is a construction management software that aims to provide all of these functionalities and more to bring out the best outcomes for a project. Enquire here today, to learn more about Wunderbuild and start your free trial.