In Australia’s ever-evolving construction landscape, builders continuously search for ways to innovate, streamline operations, and, critically, reduce waste. Enter the philosophy of Lean Construction: a strategy aiming to trim the fat from building processes. While originally inspired by manufacturing, especially the Toyota Production System, Lean Construction adapts these principles to the intricacies of constructing buildings, infrastructure, and more.
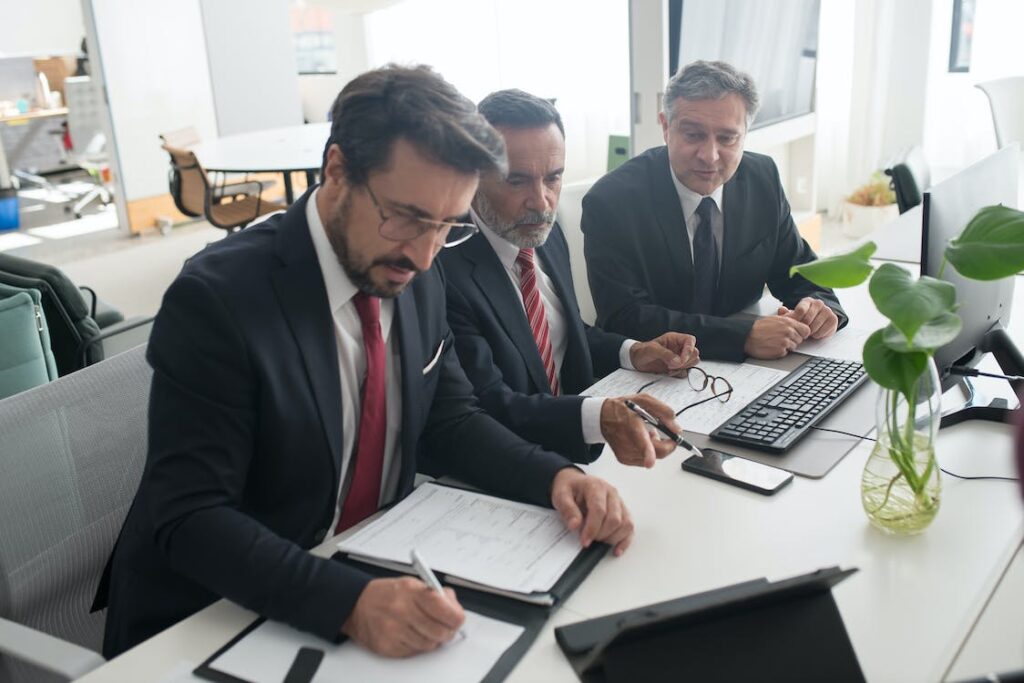
Why Lean Construction Makes Sense for Australia
Australia’s construction sector booms, with projects stretching from sprawling urban high-rises in Sydney to expansive infrastructure works in regional Queensland. However, with growth comes challenges. We’ve all seen delayed projects, costs that balloon beyond original estimates, and unnecessary waste — both in materials and human effort. Lean Construction directly addresses these pain points.
Firstly, we need to dispel a common misconception. ‘Lean’ doesn’t equate to skimping on materials or cutting essential processes. Instead, it centres on maximising value for customers by minimising waste.
The Core Tenets of Lean Construction
Defining Value from a Client’s Perspective: What do our clients actually want? Before swinging the first hammer or laying the first brick, we need to understand and define what ‘value’ means for every project. By aligning our objectives with those of our client, we ensure that every effort pushes towards the same goal.
Mapping the Value Stream: Every project involves countless steps, from initial planning to the final handover. By meticulously mapping out each process, we can identify — and subsequently eliminate — any activity that doesn’t add value.
Ensuring Continuous Workflow: Disruptions and halts in construction projects aren’t just inconvenient; they bleed money and time. Lean Construction emphasises the importance of a continuous, uninterrupted flow of work.
Using a Pull Approach: Traditional construction often uses a ‘push’ strategy — based on what we think might happen. Lean shifts this paradigm. Instead of pushing tasks according to predictions, a ‘pull’ system responds to the project’s real-time needs, ensuring that we deploy resources only when and where we genuinely need them.
Striving for Perfection: Complacency is the enemy of efficiency. Adopting Lean Construction means we’re always on the lookout for improvements, always tweaking, adjusting, and refining our processes to approach perfection.
The Tangible Benefits Down Under
For Aussie builders, adopting Lean Construction translates into:
Cost Savings: It’s straightforward — less waste means lower costs. Optimal material use, streamlined processes, and reduced reworks can save substantial amounts on the bottom line.
Faster Project Completion: When a project runs like a well-oiled machine, with every task flowing seamlessly into the next, delays diminish, and completion dates come sooner.
Higher Quality Outputs: With a clear focus on value and an emphasis on continuous improvement, the end products naturally meet higher quality standards.
Sustainability: In a country where the Great Barrier Reef faces environmental threats and bushfires remind us of nature’s power, sustainable construction isn’t just a buzzword. By reducing waste, Lean Construction supports a more sustainable Australian future.
Satisfied Clients: Projects that finish on time, adhere to budgets, and exceed quality expectations? It’s a sure-fire recipe for delighted clients, leading to strong, ongoing business relationships.
Challenges in Transitioning to Lean
While the advantages are evident, the transition to a Lean Construction model isn’t without hurdles:
Cultural Change: Long-standing practices die hard. Moving to Lean Construction requires every team member, from site managers to casual labourers, to adapt to a fresh approach. This calls for comprehensive training and, importantly, a shift in mindset.
Supply Chain Integration: It’s not just the immediate construction team that needs to adapt. Sub-contractors, material suppliers, and even stakeholders need to be on board with the Lean philosophy.
Managing the Learning Curve: As with any new system, there will be teething problems. Expecting immediate perfection can lead to disappointment. Instead, a commitment to understanding, refining, and iterating is crucial.
Taking the Leap to Lean
While the benefits of Lean Construction shine brightly, taking that initial step towards its implementation is critical. It’s about investing today for a streamlined tomorrow. Here’s how Australian construction entities can begin this transformative journey:
1. Education and Training: Knowledge remains the cornerstone of change. Companies must invest in training sessions, workshops, and even external courses. Engaging with experts in the field can offer guidance and share experiences, helping teams get a real grasp of Lean principles and their practical application.
2. Engage Every Level: From top-level management to on-site workers, everyone plays a role in this change. Management must showcase their commitment, serving as champions for Lean’s adoption. They should articulate its benefits clearly, explaining how it makes jobs more manageable, reduces unnecessary work, and leads to more successful project outcomes.
3. Pilot Projects: Instead of overhauling every ongoing project, companies might consider starting with pilot projects. This means selecting a particular project (preferably a smaller one) and applying Lean principles to it. These pilots serve as testing grounds, allowing teams to identify challenges, make necessary adjustments, and learn in a relatively controlled environment.
4. Collaborative Planning Sessions: The success of Lean relies heavily on collaboration. Regularly hosting collaborative planning sessions, where all stakeholders come together to discuss the project’s status, upcoming tasks, and potential roadblocks, can ensure smoother task transitions and better resource allocation.
5. Invest in Technology: Modern problems require modern solutions. Thankfully, a myriad of software tools now supports Lean Construction. From project management tools that align with the ‘pull’ planning approach to software that offers real-time data analysis, the tech landscape is ripe for exploration. By integrating technology, Australian construction firms can optimise their Lean strategies.
6. Feedback and Refinement: Post-project reviews are invaluable. After completing a Lean project, teams should come together to reflect on what went well and where they faced challenges. This feedback loop ensures that with every project, the company becomes more adept at using Lean methodologies.
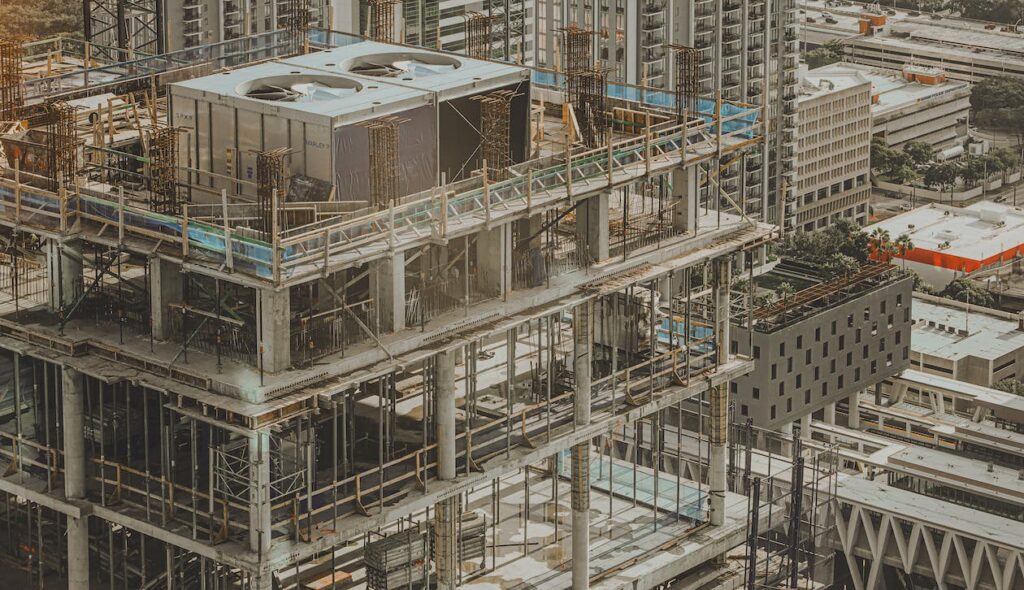
The Australian Context: Lean’s Significance
In the broader Australian context, where there’s a massive push towards sustainable living, environmentally friendly practices, and a deep-seated respect for the indigenous land, Lean Construction finds a fitting home. It’s not just about trimming costs or speeding up projects. It’s about honouring the country’s ethos of respect — respect for the client’s vision, the worker’s effort, and the land’s bounty.
Moreover, as Australia positions itself as a global leader in various sectors, construction must not lag. International businesses, when looking to set up in Australia, will scout for construction partners who align with their global standards. Lean, with its universal appeal and globally recognised principles, positions Australian builders as prime candidates for such partnerships.
Future Gazing: What Lies Ahead
The construction sector, as with any other, will continue evolving. We’re on the cusp of seeing more tech integration, with AI, augmented reality, and machine learning set to play more prominent roles. In such an environment, Lean serves as a solid foundation, ensuring that while we embrace the future, we remain grounded in efficiency and value.
Lean Construction, therefore, isn’t a mere methodology. For the Australian construction sector, it could very well be the bridge to a future where efficiency, sustainability, and excellence are not just buzzwords, but everyday practices. The call to action for Australian builders is clear: Embrace Lean today, and lay the foundation for a brighter, better, and more efficient tomorrow.
Embracing Lean in Diverse Australian Landscapes
Australia’s diverse landscapes — from its bustling cities to serene coastal areas and rugged outbacks — offer unique challenges and opportunities for construction. Each environment requires a nuanced approach, yet the principles of Lean can be universally applied.
1. Urban Constructions: In cities like Melbourne, Brisbane, and Adelaide, space is at a premium. Urban projects often need to juggle tight sites, busy surroundings, and the constant buzz of city life. Lean Construction helps manage these challenges. By optimising processes, reducing wastage, and ensuring a continuous flow of tasks, urban constructions can swiftly progress, minimising disruptions for the city’s inhabitants.
2. Coastal Builds: Australia boasts a vast coastline. Projects along these areas, be it for residential, commercial, or tourism purposes, must consider the unique environmental factors: the salt-laden air, winds, and potential floods. Here, Lean ensures that every material used, every process adopted, is in line with the coastal context, maximising longevity and minimising environmental impact.
3. The Outback Challenge: Constructing in Australia’s outback is no small feat. The remoteness, harsh climate, and limited access to resources present unique challenges. Adopting Lean in such scenarios ensures that every resource, be it material or human, is utilised to its fullest, reducing the need for frequent replenishments or transport — a critical factor in such isolated terrains.
Maintaining Cultural Integrity with Lean
One cannot discuss construction in Australia without acknowledging the rich Indigenous heritage. Respecting the cultural significance of lands, understanding local histories, and engaging with Indigenous communities is paramount. Lean principles, when applied thoughtfully, can aid this engagement.
By defining value from a client’s and community’s perspective, builders can ensure that projects respect local sensibilities. This might mean preserving certain landmarks, using indigenous art or designs, or even adopting locally preferred construction methods. The value stream can be tailored to integrate traditional techniques, ensuring that while we adopt modern methodologies, we don’t sideline cultural significance.
Tackling Labour Challenges with Lean
Australia’s construction industry, like many sectors, faces labour challenges. The intermittent nature of construction jobs, paired with the skills shortage in specific trades, can sometimes hamper progress. Lean, with its emphasis on continuous workflow and efficiency, can help mitigate these challenges.
By ensuring that every worker’s time is optimally utilised, Lean reduces idle periods. This not only accelerates project timelines but also ensures that workers derive maximum value from their engagement, potentially leading to increased job satisfaction and reduced turnover.
Elevate Your Construction Management with Wunderbuild
Harness the power of Wunderbuild, the premier construction management software that seamlessly integrates takeoffs, estimations, interactive Gantt chart scheduling, and more into one unified platform. With features ranging from job and lead management to selections, checklists, and a handy mobile app, it’s the tool that every construction professional needs. Ready to transform your building process? Find out more here.